Operators may encounter various faults when using water well drilling rigs. Knowing these common problems and their solutions will help them respond quickly and reduce downtime.
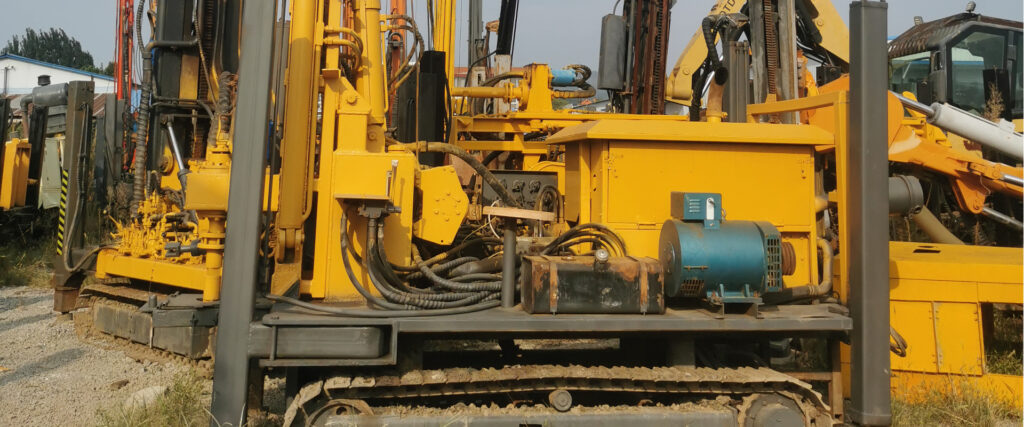
First, excessive wear is a common problem for many users.
This is usually caused by poor drill bit material or improper operation. The solution is to regularly inspect the wear of the drill bit, replace it with high-quality drill bits when necessary, and adjust the drilling parameters accordingly.
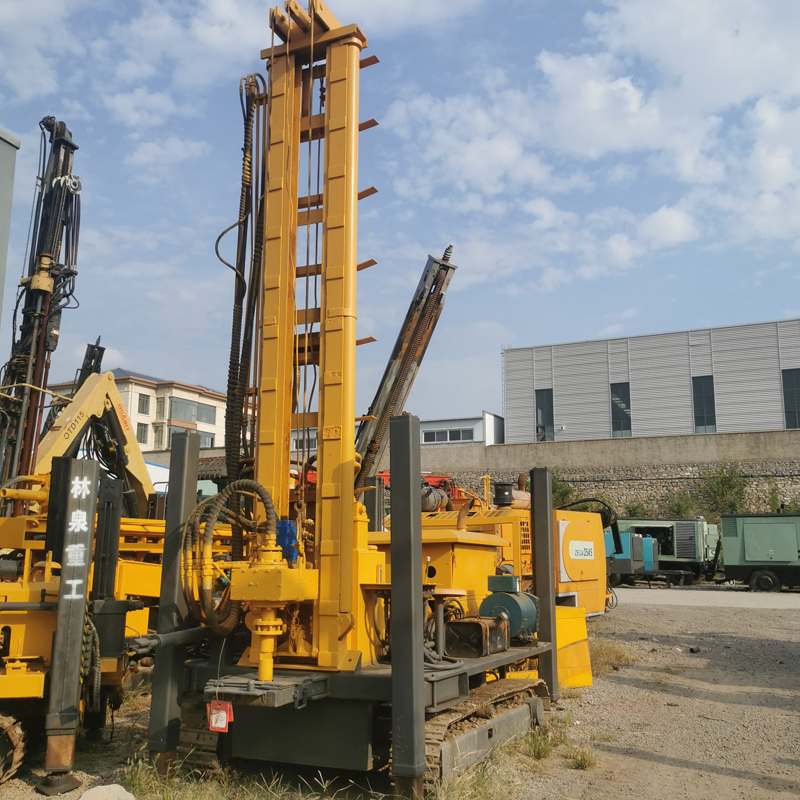
Second, the drill bit stuck problem is also a common fault, especially when drilling hard rocks.
A drill stuck will cause the equipment to fail to operate normally and increase maintenance costs. To avoid drill stuck, operators should maintain appropriate drilling speed and pressure, and regularly clean the mud and drill cuttings in the borehole. If a drill becomes stuck, stop drilling immediately, gently rotate the drill, and attempt to pull out the equipment.
Third, hydraulic system failure is also an area that needs attention.
The hydraulic system is the core part of the normal operation of the drilling rig, and any leakage or insufficient pressure will affect performance. Regularly check the hydraulic oil’s status and the hydraulic pipeline’s connection to ensure that it is working properly. If there is a leak, the damaged parts should be replaced in time.
Finally, electrical system problems may also cause the rig to not work properly.
Check the electrical lines and control panel to ensure good connections to avoid malfunctions caused by poor contact. If necessary, ask professionals to perform a comprehensive inspection and maintenance of the electrical system.
By identifying and resolving these common faults promptly, you can ensure the efficient operation of the used water well drilling rig and improve work efficiency and safety.